Case Study
Optimising inbound material planning and in-plant logistics
This case study explores how strategic planning and implementation helped a leading Indian automobile manufacturer to achieve cost reduction and efficiency gains.
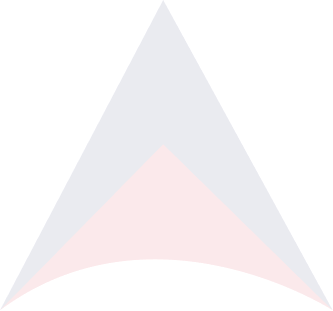
Expectation
The client aimed to streamline their supply chain by optimising inbound material planning and in-plant logistics. Their primary goal was to minimise waste and achieve cost reduction through improved efficiency.
Expectation
The client aimed to streamline their supply chain by optimising inbound material planning and in-plant logistics. Their primary goal was to minimise waste and achieve cost reduction through improved efficiency.
Approach

Inbound Material Planning
We focused on synchronised deliveries, resource optimisation, and streamlined workflows to ensure a steady flow of materials, efficient unloading at docks and optimal workforce allocation.

In-Plant Logistics
We introduced a pull system for material movement, assigned dedicated line runners for material feeding, and implemented a GPS-based tracking system for trucks. This ensured parts availability on the assembly line, improved responsiveness, and minimised time wasted for trucks within the plant.
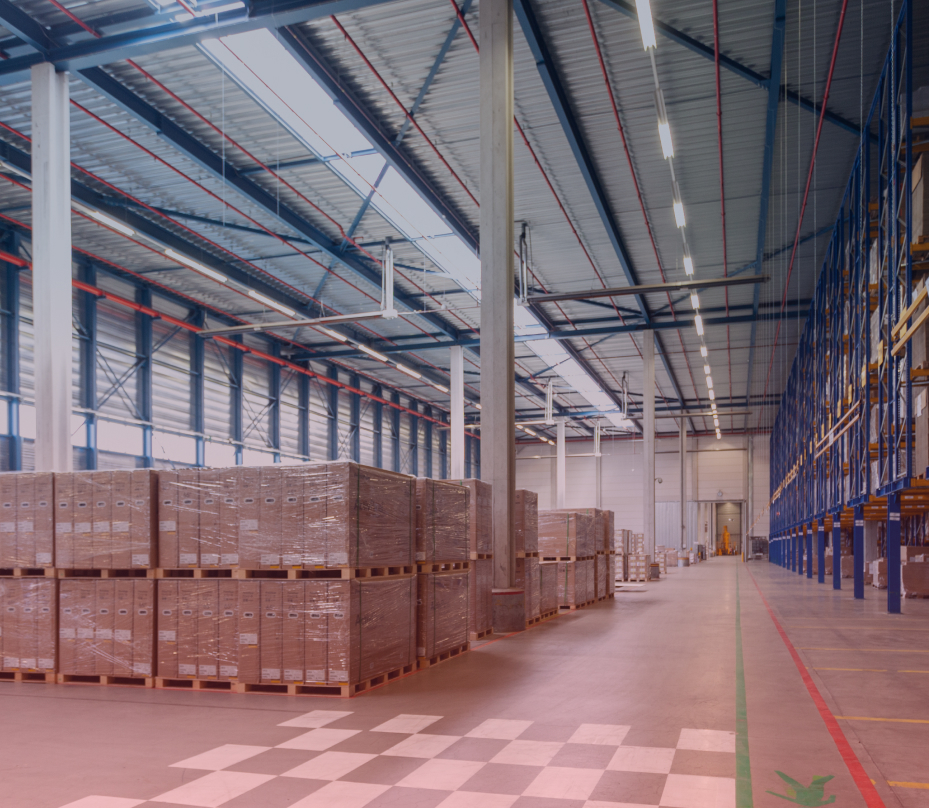
Outcome
Reduced Inventories
Minimised Line Stoppages
Improved Efficiency
Optimised Space Utilisation
Enhanced Workforce Utilisation
Improved Traceability
Efficient processes reduced opening inventory by 20%.
Ready parts availability minimised line stoppages.
We achieved a 40% peak traffic reduction and a 50% decrease in average waiting time for trucks.
We achieved a 20% reduction in storage space requirements.
Better allocation of tasks led to enhanced workforce utilisation.
Trucks could be traced efficiently within the plant premises due to streamlined operations.