Case Study
Supercharging spare parts management with unit packaging
The client – an OEM manufacturer had recurring issues with managing numerous SKUs as per orders received. We helped them with a streamline packaging process, which significantly boosted efficiency and customer satisfaction.
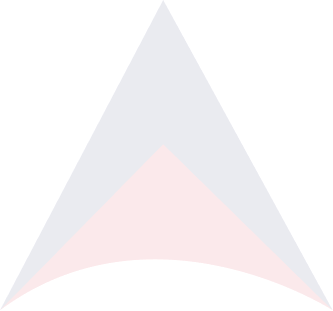
Expectation
The client faced frequent issues with the single packing of all SKUs. This led to mismatched products, tampered packaging, extended turnaround times, and ultimately, brand dilution.
Expectation
The client faced frequent issues with the single packing of all SKUs. This led to mismatched products, tampered packaging, extended turnaround times, and ultimately, brand dilution.
Approach

Strategic Hub
We identified FTWZ as the most effective solution, creating a central hub for seamless import, storage, and re-export.

Comprehensive Services
Our scope encompassed movement from ports/airports to the FTWZ, empty container repositioning, handling and container unloading, customs brokerage (inbound/outbound), quality control, and diverse storage options.

Efficient Distribution
We implemented cross-docking and loading operations for swift transportation to over 30 international locations.

Innovative Unit Packaging
We designed a meticulous unit packaging system, ensuring each SKU had its own designated packaging.

Tamper-Proof Security
We prioritised security with tamper-proof packaging for both individual units and minimum order quantities (MOQ).

Crystal Clear Labeling
Each unit received clear and detailed labelling, eliminating confusion and facilitating accurate order fulfilment.

Receipt Stage Integration
The unit packaging process is seamlessly integrated with the receipt stage for import consignments. Incoming inventory received a Goods Received Note (GRN) only after undergoing unit packaging.
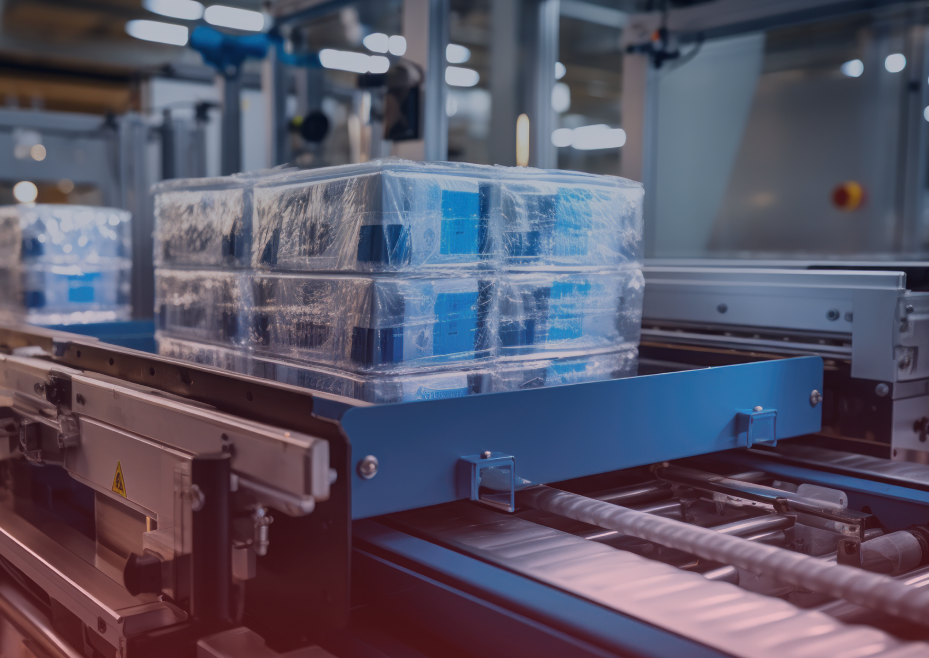
Outcome
Accurate Supplies
Faster Turnaround Time
Cost Consciousness
Unit packaging dramatically improved dispatch accuracy, minimising errors and ensuring customers receive the correct parts promptly.
By streamlining processes, turnaround times for servicing end users improved significantly, leading to increased customer satisfaction.
The new system also yielded the additional benefit of inventory cost reduction.
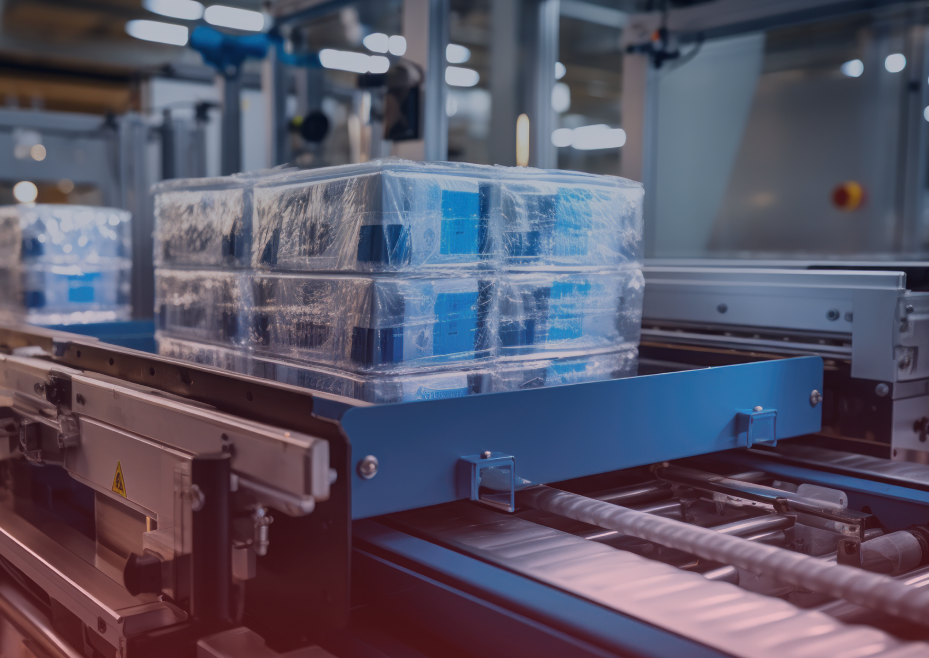
Outcome
Accurate Supplies
Faster Turnaround Time
Cost Consciousness
Unit packaging dramatically improved dispatch accuracy, minimising errors and ensuring customers receive the correct parts promptly.
By streamlining processes, turnaround times for servicing end users improved significantly, leading to increased customer satisfaction.
The new system also yielded the additional benefit of inventory cost reduction.